While bucket trucks and aerial lift equipment may not always grab headlines, innovation in this space is quietly but powerfully transforming utility operations. Today’s top aerial lift advancements don’t just improve safety—they drive productivity, reduce maintenance costs, and cut fuel usage, all of which directly lift a utility company’s bottom line.
How Aerial Lift Innovations Drive ROI
✅ Faster Setup Times
New outrigger systems and tail-shelf access features let crews get to work faster—translating to more job completions per day.
✅ Lower Fuel Costs
Hybrid and electric models with auto shutoff features reduce idling and save thousands in fuel expenses annually.
✅ Reduced Maintenance Downtime
Easy-access service compartments and greaseless bushings mean less time in the shop and more time on the job.
✅ CDL Not Required
Lighter chassis options allow for high-reach performance without requiring a CDL driver—saving on labor costs.
✅ Fewer Injuries
Advanced safety features and stable designs lower the risk of costly on-site incidents.
Everything starts with safety.
“You can’t lose sight of the fact that, on average, 26 lineworkers lose their lives each year,” said Jeff Postlethwaite, Engineering Manager at PALFINGER North America, a leading manufacturer of bucket trucks and cable placers, aerial platforms, and other equipment. “So, while innovation and the latest bells and whistles are exciting, we remain focused on making products that are as ergonomic, stable, and reliable as possible so lineworkers can be safe and efficient.”
“Performance, productivity, and safety are among the top concerns of electric utilities,” added Tyler Schwingler, Product Marketing Manager at Terex Utilities, a manufacturer of bucket trucks and other equipment. “By staying engaged with customers, we seek to apply technology in practical ways to improve the user’s experience.”
For instance, Terex Utilities’ Optima Series, ideal for distribution work, is built on the foundation of its popular Hi-Ranger bucket trucks. Product improvements include greater payload capacity, better boom speeds, enhanced side reach and ground access, and improved maintenance access and reliability. In the transmission segment, TL Transmission Series bucket trucks have been designed to increase uptime and reliability with commonality among parts. “These units are also typically mounted on a lower-cost, lighter-weight chassis compared to traditional transmission aerials,” Schwingler pointed out.
Stability That Reduces Downtime and Injuries
Postlethwaite said utility workers often remark about how “stable” PALFINGER machines feel. That’s a bottom line-boosting benefit because safety is enhanced. Additionally, workers will operate more comfortably and, thus, efficiently. There are a couple of design features that play into this.
“One factor is how rigid the understructure is,” Postlethwaite explained. “It starts with the design of the base and moves to the boom structure. Different shapes provide more rigidity than others.”
The second factor is the control system. If an operator lets go of the control, a power ramp-down can be programmed in so the equipment slows down less aggressively. For example, if the lift is rotating around and suddenly stops, Postlethwaite said it settles smoothly and feels more secure.
A specialized bucket truck PALFINGER introduced in March 2025 is the PB 38 AT P Cable Placer. Postlethwaite said cable placers have historically been a bit cumbersome to operate. So PALFINGER implemented a design change that enables linemen to access the bucket from the tail shelf.
“Easier access makes things safer,” Postlethwaite emphasized. “This also helps improve the bottom line. Instead of having to operate from the lower controls to get the basket down on the ground, and then get into the basket to start doing the job, linemen can just walk right up on the tail shelf, get in the basket, and go to work. That saves time.” And less time per task means more jobs completed per day – delivering measurable productivity gains.
Also on the safety front, Alan Berry, Sales Manager for Bucket Trucks & Digger Derricks at Fouts Commercial Vehicles in Milledgeville, Georgia, a manufacturer of specialized commercial vehicles and a dealer for Versalift, said one of the most impactful innovations he’s seen is Versalift’s TruGuard Safety System. The foundation of TruGuard is a uniquely engineered polymer with high dielectric insulation properties and strength.
“By completely isolating the work platform, TruGuard protects all control handles at the platform, including control handles at the upper control, hydraulic tool power ports, and the console area itself,” said Berry. TruGuard is also resistant to dirt and grime, which helps close a safety gap left by systems that merely rely on plastic handles to isolate the upper controls.
Berry said another important Versalift innovation has been SlopeMax, which measures the slope angle of the surface and boom. SlopeMax then limits horizontal reach via the lower boom function whenever necessary to improve safety.
Next-Level Productivity Without Upgrading Truck Classes
According to Berry, utilities are also looking for maximum productivity — without always having to jump up a truck class.
“A higher reach on a smaller chassis helps keep weight down, making it easier for utilities to put workers in the truck because the driver doesn’t need a CDL,” Berry said. “An example is Versalift’s VST-55-HDI articulated telescopic bucket truck. It has a nearly 60-foot working height, and is based on the Ford F-600 chassis (Class 6). Versalift’s towers feature a lighter design with fewer internal moving parts, helping keep working weights down without compromising safety.”
Posi+ has given utility workers a productivity advantage by implementing computer-controlled valves (Hawe brand) on its cable placers. This valve system allows the speed of each function to be controlled independently. Additionally, the valves can be programmed to mimic the controls of other equipment brands that certain line workers may be more familiar with. “That makes operation more comfortable, and also reduces training time,” said Dan O’Connell, Director of Sales & Marketing at Posi+.
The Posi+ Model 700 and 800 Cable Placers combine computer-controlled valves and an oversized pump, allowing operators to handle three functions at the same time: go up, rotate, and squirt out.
“The computer prioritizes the area where the machine needs fluid to be productive,” O’Connell said. “An added advantage is that the computer also controls the RPM of the engine. Sometimes line workers feel the desire to go as fast as possible, so RPMs are always up. When there’s no need for pressure or fluid to flow, the computer turns down the RPMs. That helps save money by reducing fuel usage.”
Another unique feature on Posi+ cable placers is a camera system that’s mounted on the lower boom, as opposed to the dashboard. “This helps the driver see exactly what the lineman in the bucket is going to anticipate,” O’Connell said. “Then the driver can go faster when things are clear, slow down when they encounter branches, etc., and then increase speed again. That helps maximize productivity while maintaining safety.”
One more notable innovation that enhances both safety and productivity is Elliott Equipment Company’s EZ-Crib Outriggers found on its E-Line Electric Utility Transmission Aerials. EZ-Crib Outriggers improve job setup efficiency by providing an additional 30 inches of penetration. That not only enhances setup on uneven terrain but also reduces the number of cribbing a crew needs to use at the truck level. That takes a lot of time out of the setup process, while also sparing workers from having to lug so many heavy ground boards around.
Fuel-Saving Tech That Cuts Operating Costs
As Posi+ just touched on, a great way to boost the bottom line is to reduce fuel costs. There are plenty of examples of how this is taking place.
The Bluelift B72 Aerial Lift by Ruthmann Reachmaster is a hybrid machine, capable of being powered by a combination of lithium battery power and gas or diesel. Additionally, the B72 features engine auto start/stop, where the engine shuts down if no control lever has been pulled in more than 20 seconds. The company says these features help users cut down on fuel usage.
Terex has been helping customers reduce fuel consumption too.
“Many Terex bucket trucks offer an optional Hypower SmartPTO by Viatec,” Schwingler said. “The SmartPTO reduces idling, and also minimizes noise and air pollution by utilizing stored plug-in electric power to operate the equipment.”
Following extensive field testing, Schwingler said line workers have reported equivalent performance compared to an engine-powered PTO. “Additionally, not having the chassis engine running decreased jobsite sound pollution, allowing for better verbal communication,” Schwingler said.
One of Terex Utilities’ more recent innovations is an all-electric bucket truck introduced in 2022, which provides an option for pivoting away from fossil fuels completely. The truck has an Optima 55-foot aerial powered by a SmartPTO on an International eMV Series chassis. Now, through a partnership with Mack Trucks, Terex is introducing the next generation of a zero-emission bucket truck. Terex has installed its Optima HR55 aerial device powered by the SmartPTO on the Mack MD7 Electric chassis.
“Preliminary testing revealed up to 1.5 times enhanced range capabilities compared to other Class 6/7 medium-duty electric chassis bucket trucks, with double the payload capacity on the rear axle,” Schwingler said. “The Terex aerial device, powered by the SmartPTO, operates independently of the Mack MD7 Electric chassis. That helps ease range anxiety, and allows utility crews to operate the boom and outriggers for a normal workday without taking away charge from the chassis.”
Low-Maintenance Designs That Reduce Service Downtime
Equipment that is easier to maintain can also improve a company’s bottom line.
“A good example is the brass bushings some manufacturers used in the past that needed to be greased,” Postlethwaite said. “PALFINGER has switched to fiber bushings, which helps save time and money because you don’t have to grease them. It also creates a safer product. You don’t have to worry about those bushings and pins locking up because they haven’t been properly greased.”
Posi+ has also taken steps to make its aerial equipment more serviceable. “Most valves tend to be buried,” O’Connell said. “Ours are in a compartment that opens right up, right in the pedestal of the machine. The worker just unbolts it and turns two levers. It saves a lot of time when something needs to be serviced.”
As these examples show, aerial lift innovations aren’t just about reaching new heights—they’re about boosting the bottom line. Whether it’s saving fuel, trimming training time, or reducing setup hassle, today’s smartest equipment delivers real ROI where it matters most: in the field, in the books, and on every jobsite.
See These Innovations Up Close at The Utility Expo 2025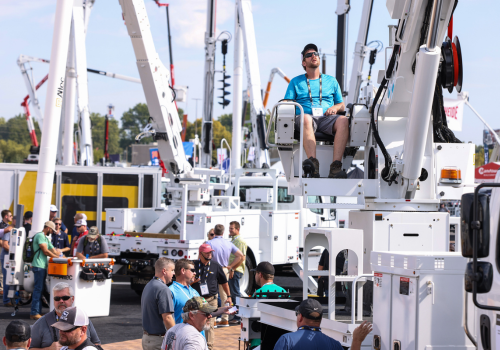
PALFINGER, Terex Utilities, Versalift, Posi+, Elliott Equipment, and other leading manufacturers will be showcasing the latest advancements and technology at The Utility Expo 2025, taking place in Louisville, Kentucky, U.S.A., October 7-9, 2025.
This is your chance to explore the latest equipment advancements in-person, talk directly with product experts, and discover new ways to improve your bottom line in the field.
Subscribe to The Utility Expo monthly newsletter to receive more industry insights like this.
Read Next
The Latest Advancements in Aerial Equipment
The AI-Powered Fleet: Safer, Smarter, More Efficient
Today’s ePTOs are Good for the Job, Good for the Environment